CR-80T Welding Rotators
✧ Introduction
80-ton conventional welding rotator is a heavy-duty piece of equipment designed for the controlled rotation and positioning of large workpieces weighing up to 80 metric tons (80,000 kg) during welding operations. This type of rotator is commonly used in industries where substantial components need to be welded, such as shipbuilding, heavy machinery manufacturing, and pressure vessel production.
Key Features and Capabilities:
- Load Capacity:
- Capable of supporting and rotating workpieces with a maximum weight of 80 metric tons (80,000 kg).
- Suitable for large industrial applications and heavy-duty components.
- Conventional Rotational Mechanism:
- Features a robust turntable or roller mechanism that allows for smooth and controlled rotation of the workpiece.
- Typically driven by high-torque electric motors or hydraulic systems to ensure reliable performance.
- Precise Speed and Position Control:
- Equipped with advanced control systems that enable precise adjustments to the speed and position of the rotating workpiece.
- Features like variable speed drives and digital controls facilitate accurate and repeatable positioning.
- Stability and Rigidity:
- Constructed with a heavy-duty frame to withstand the significant loads and stresses associated with handling 80-ton workpieces.
- Reinforced components and a stable base ensure reliability during operation.
- Integrated Safety Features:
- Safety is a key consideration, with features such as emergency stop buttons, overload protection, and safety interlocks to prevent accidents.
- Designed to provide a secure working environment for operators.
- Seamless Integration with Welding Equipment:
- The rotator is designed to work alongside various welding machines, such as MIG, TIG, and submerged arc welders, ensuring a smooth workflow.
- Allows for efficient handling and welding of large components.
- Customization Options:
- Can be customized to meet specific operational needs, including adjustments to turntable size, rotational speed, and control interfaces based on the project requirements.
- Versatile Applications:
- Ideal for a wide range of applications, including:
- Shipbuilding and repair
- Heavy machinery manufacturing
- Fabrication of large pressure vessels
- Structural steel assembly
- Ideal for a wide range of applications, including:
Benefits:
- Enhanced Productivity: The ability to rotate large workpieces reduces the need for manual handling, improving workflow efficiency.
- Improved Weld Quality: Consistent rotation and positioning contribute to high-quality welds and better joint integrity.
- Reduced Labor Costs: Automating the rotation process minimizes the need for additional labor, lowering overall production costs.
✧ Main Specification
Model | CR-80 Welding Roller |
Turning Capacity | 80 ton maximum |
Drive Load Capacity | 40 ton maximum |
Idler Load Capacity | 40 ton maximum |
Adjust Way | Bolt adjustment |
Motor Power | 2*3kw |
Vessel Diameter | 500~5000mm |
Rotation Speed | 100-1000mm/min Digital display |
Speed control | Variable frequency driver |
Roller wheels | Steel coated with PU type |
Control system | Remote hand control box & Foot pedal switch |
Color | RAL3003 RED & 9005 BLACK / Customized |
Options | Large diameter capacity |
Motorized traveling wheels basis | |
Wireless hand control box |
✧ Spare Parts Brand
1.Our 2 rotation reducer is heavy type with more than 9000Nm.
2.Both 3kw motors with fully CE approval to European market.
3.Controls electric elements are easily to find it at Schneider shop.
4.One remote hand control box or wireless hand box will be ship together.
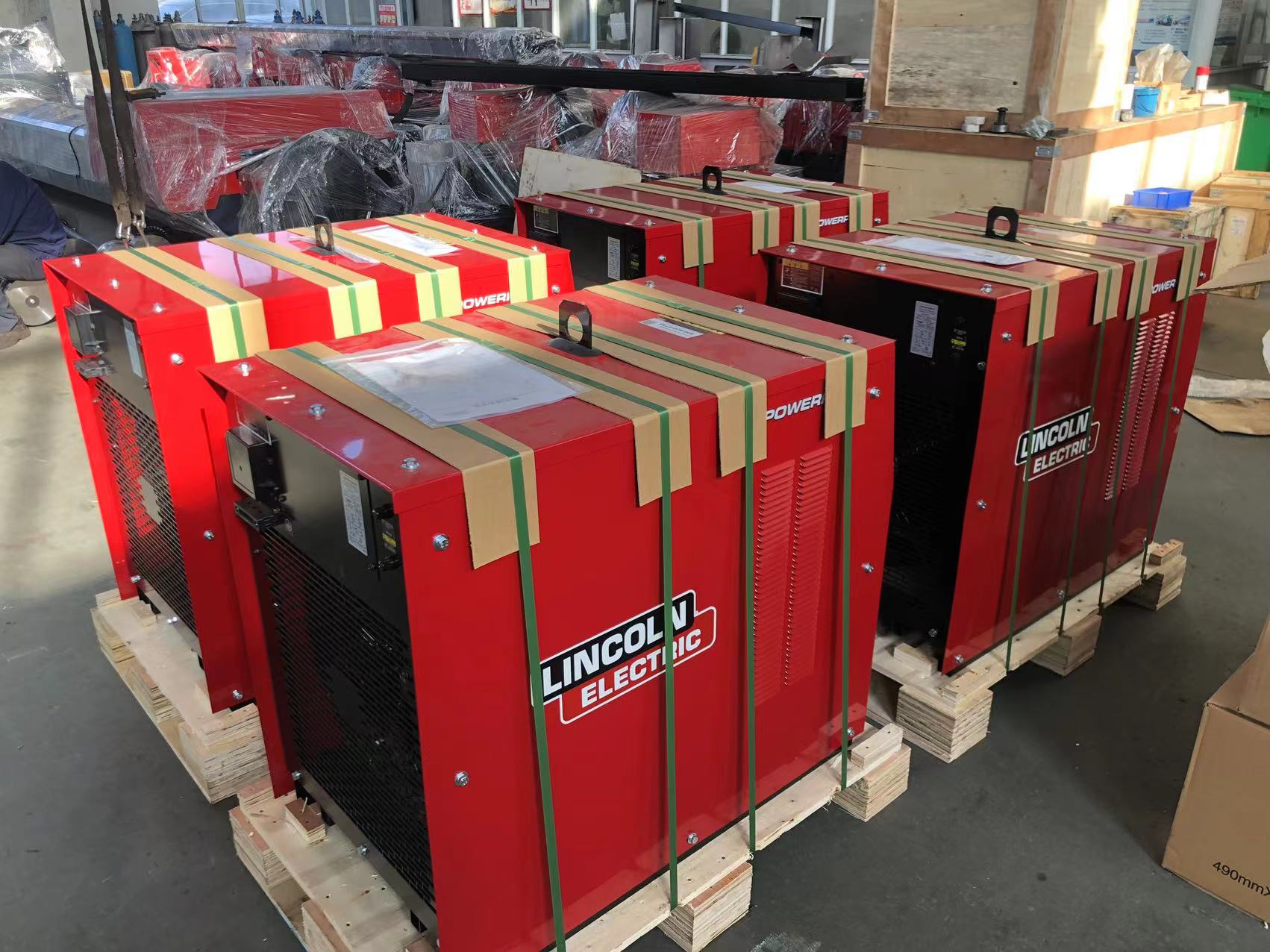
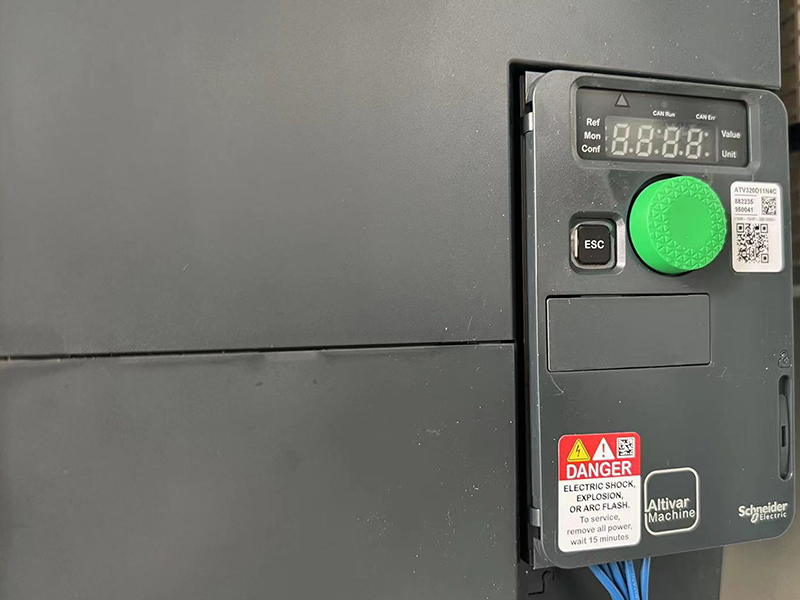
✧ Control System
1.Nomally the welding rotator with one remote hand box to control the rotation direction and adjust the rotation speed.
2.Workers can adjust the rotation speed by a digital readout on the hand box. It will be easy to get the suitable rotation speed for workers.
3.For heavy type welding rotator, we also can supply the wireless hand
4.All the functions will be available on the remote hand control box, like Rotation speed display, Forward , Reverse, Power Lights and Emergency Stop etc.
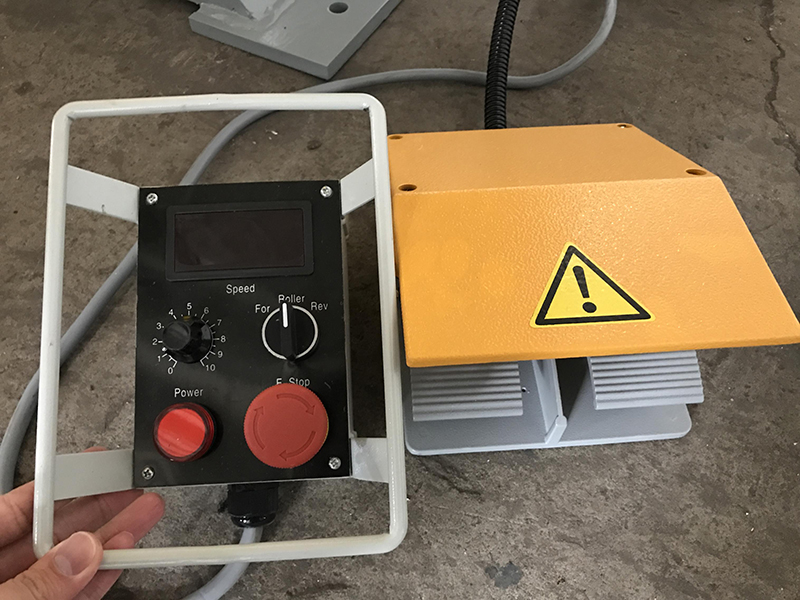


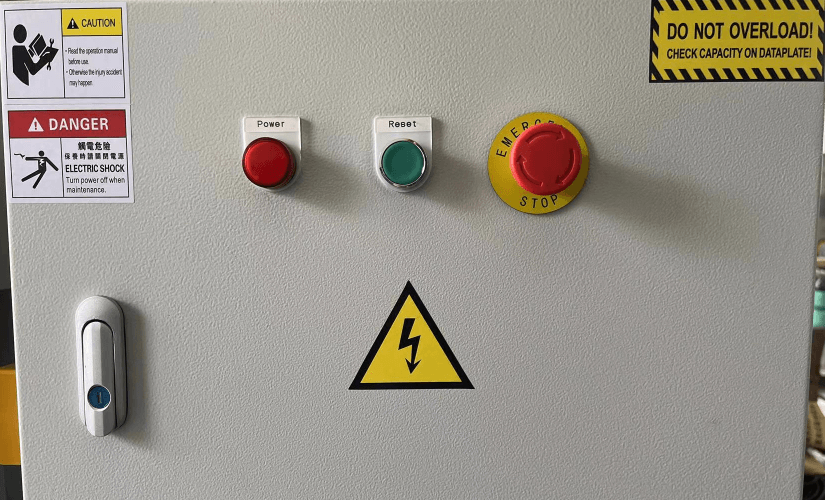
✧ Production Progress
WELDSUCCESS as a manufacturer, we produce the welding rotators from the original steel plates cutting, welding, mechanical treatment, drill holes, assembly, painting and final testing.
In this way, we will control all the production process is under our ISO 9001:2015 quality management system. And ensure our customer will receive a high quality products.
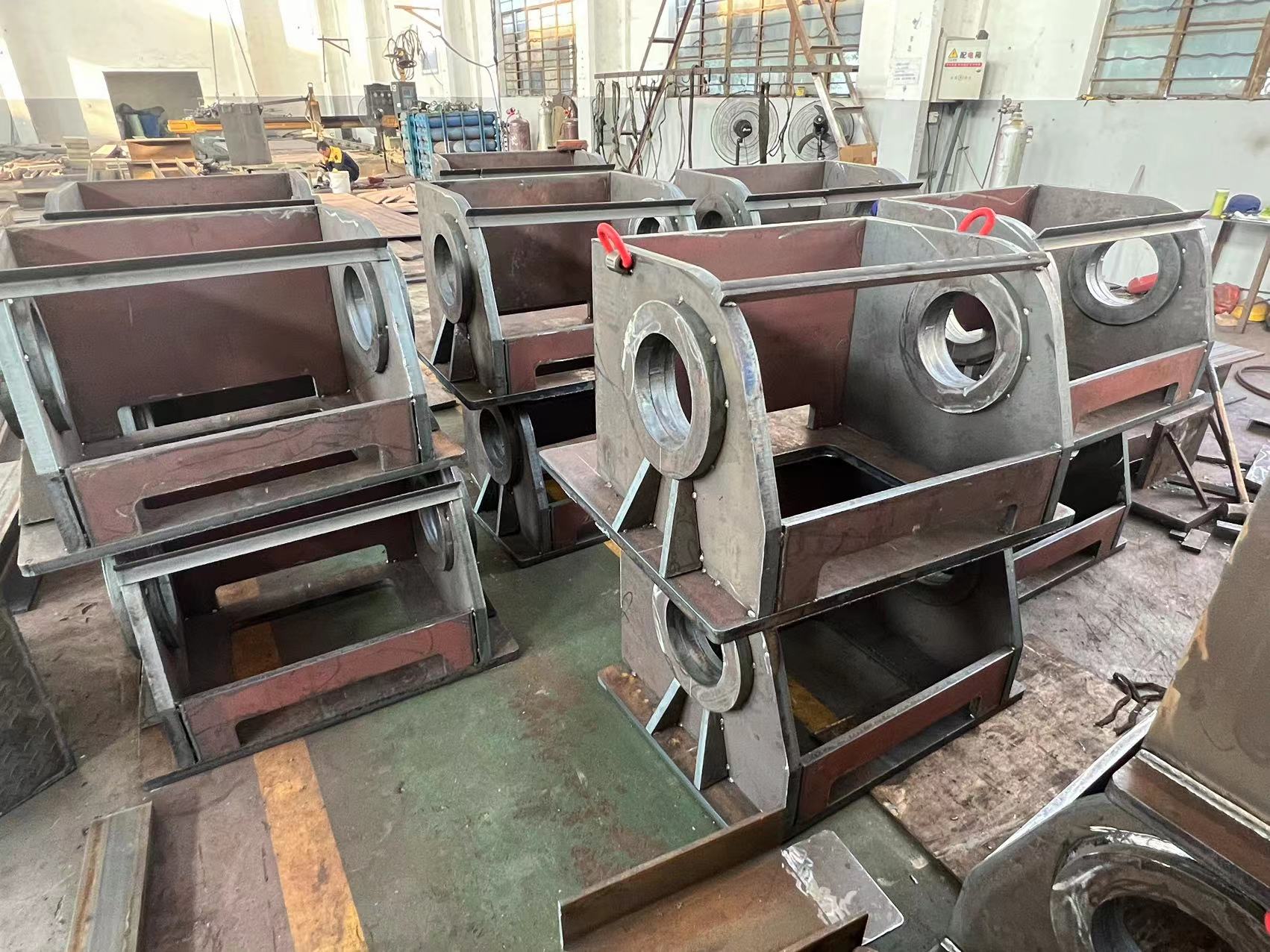
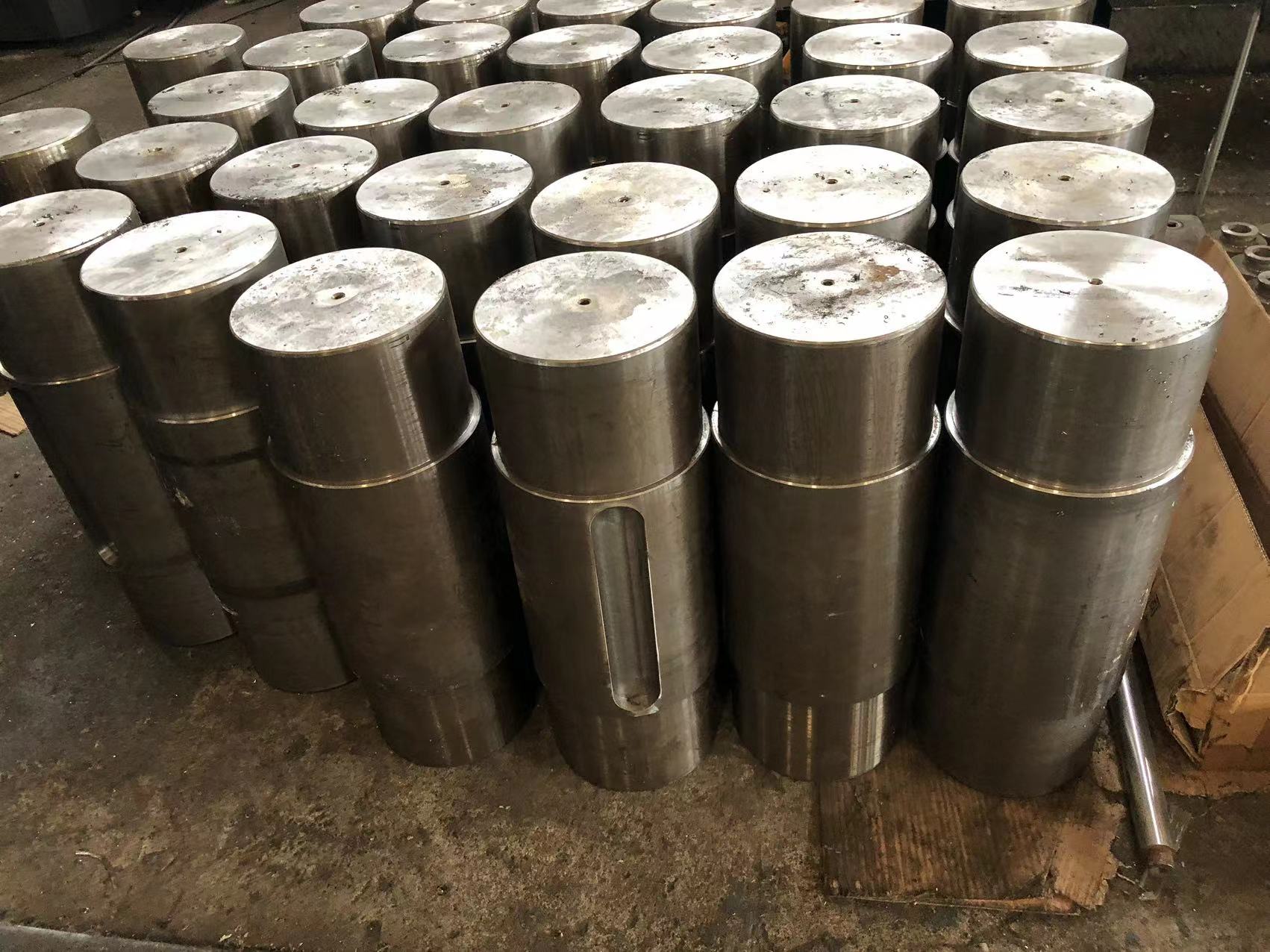
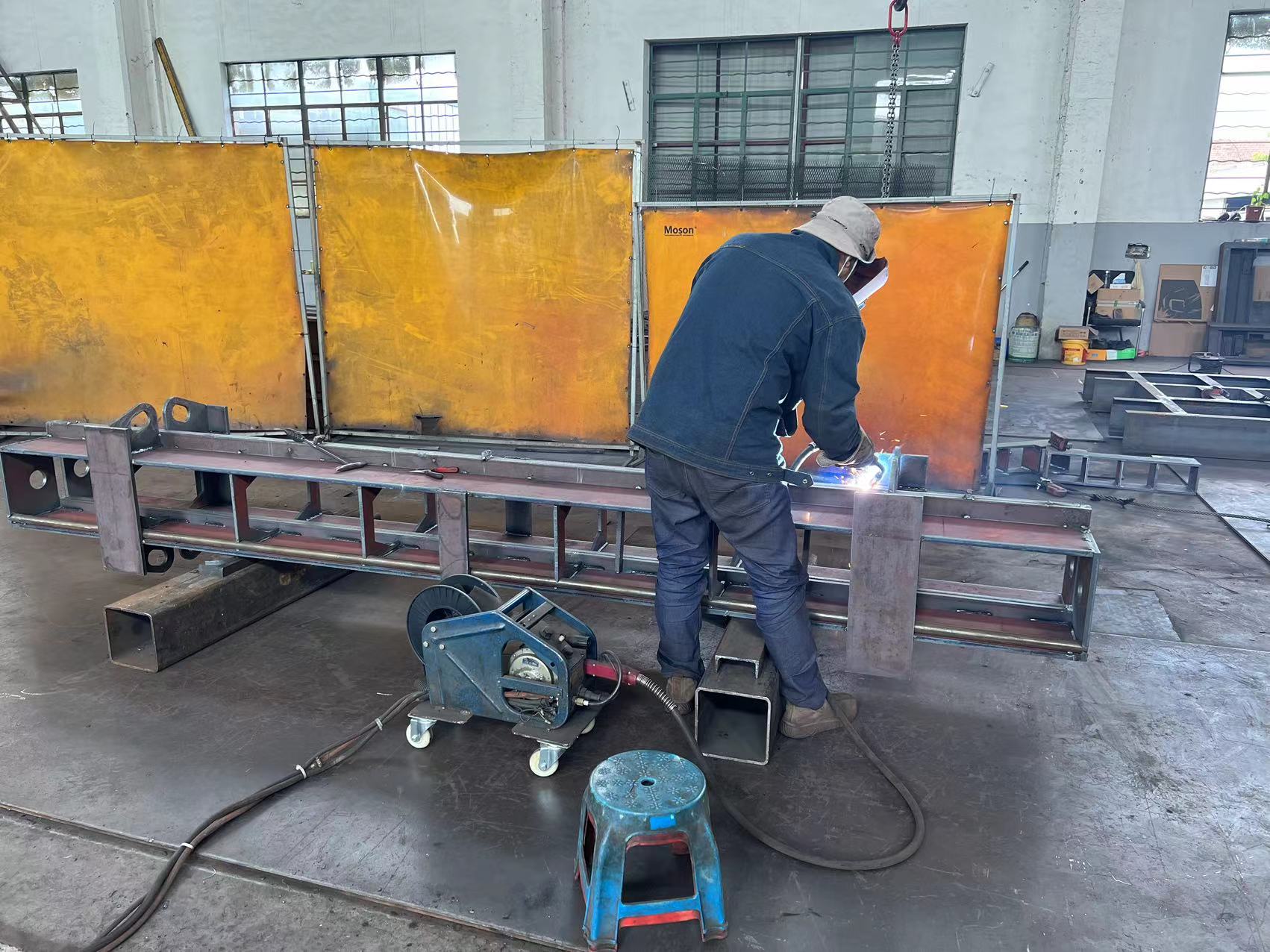
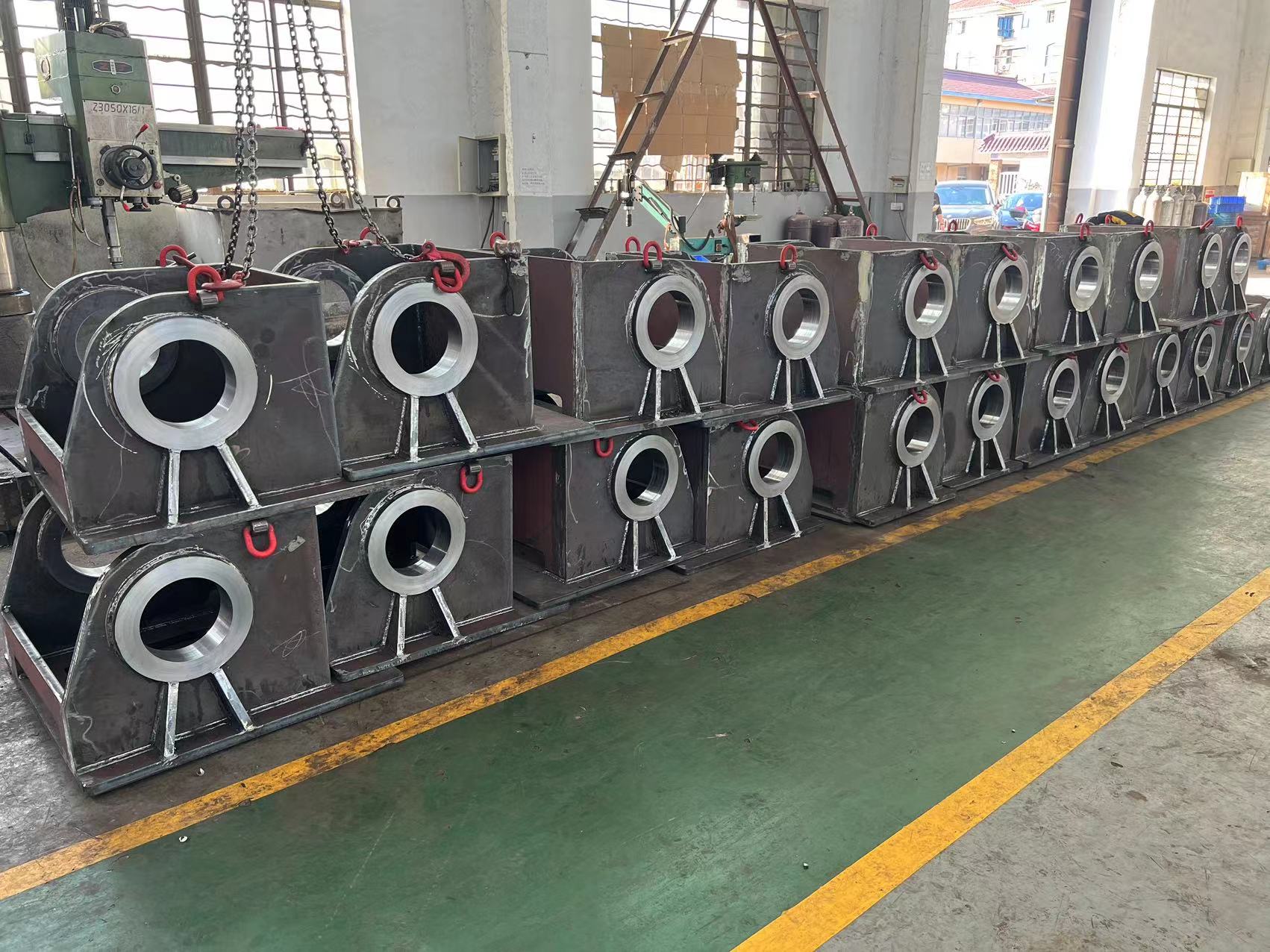
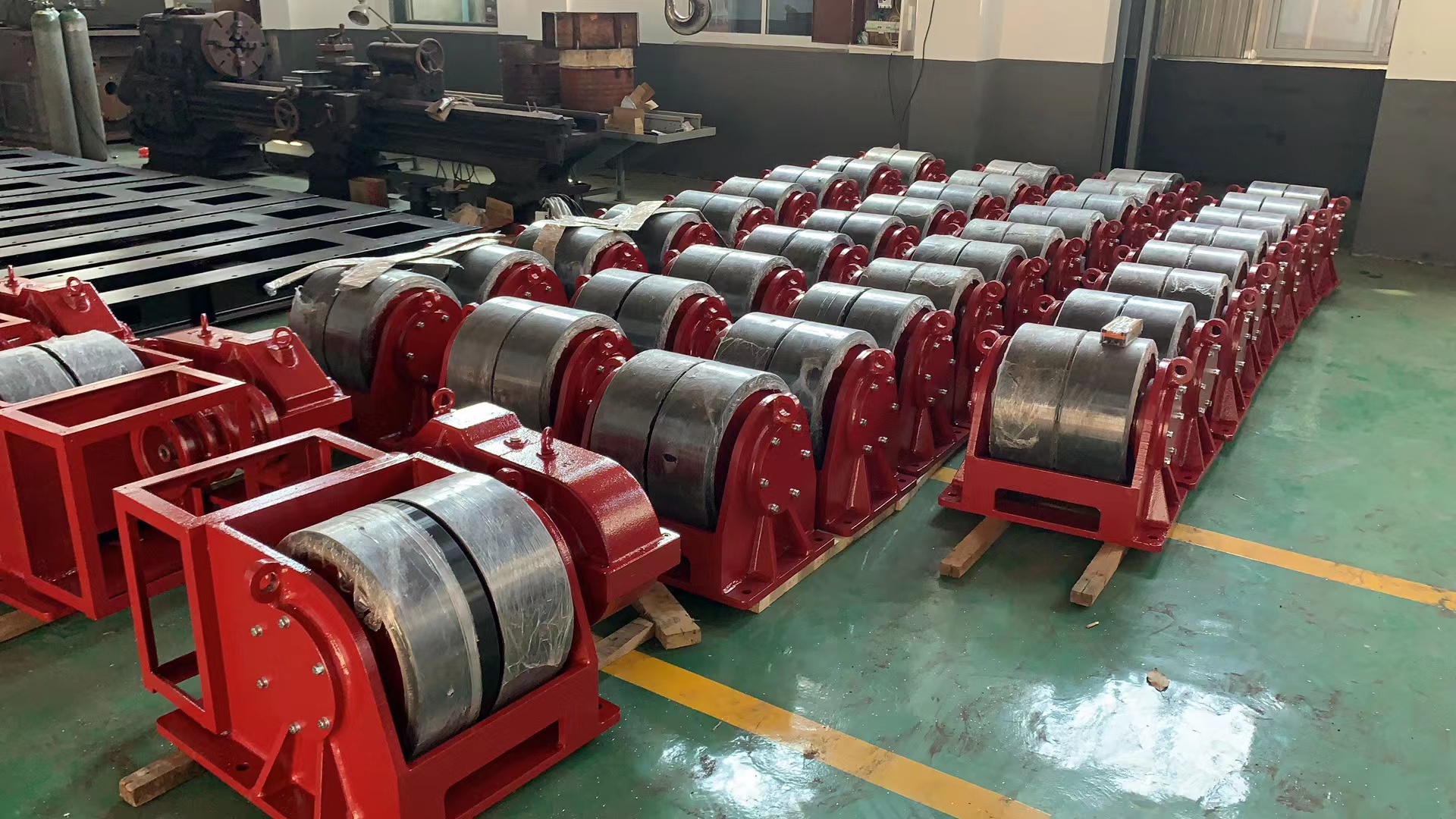
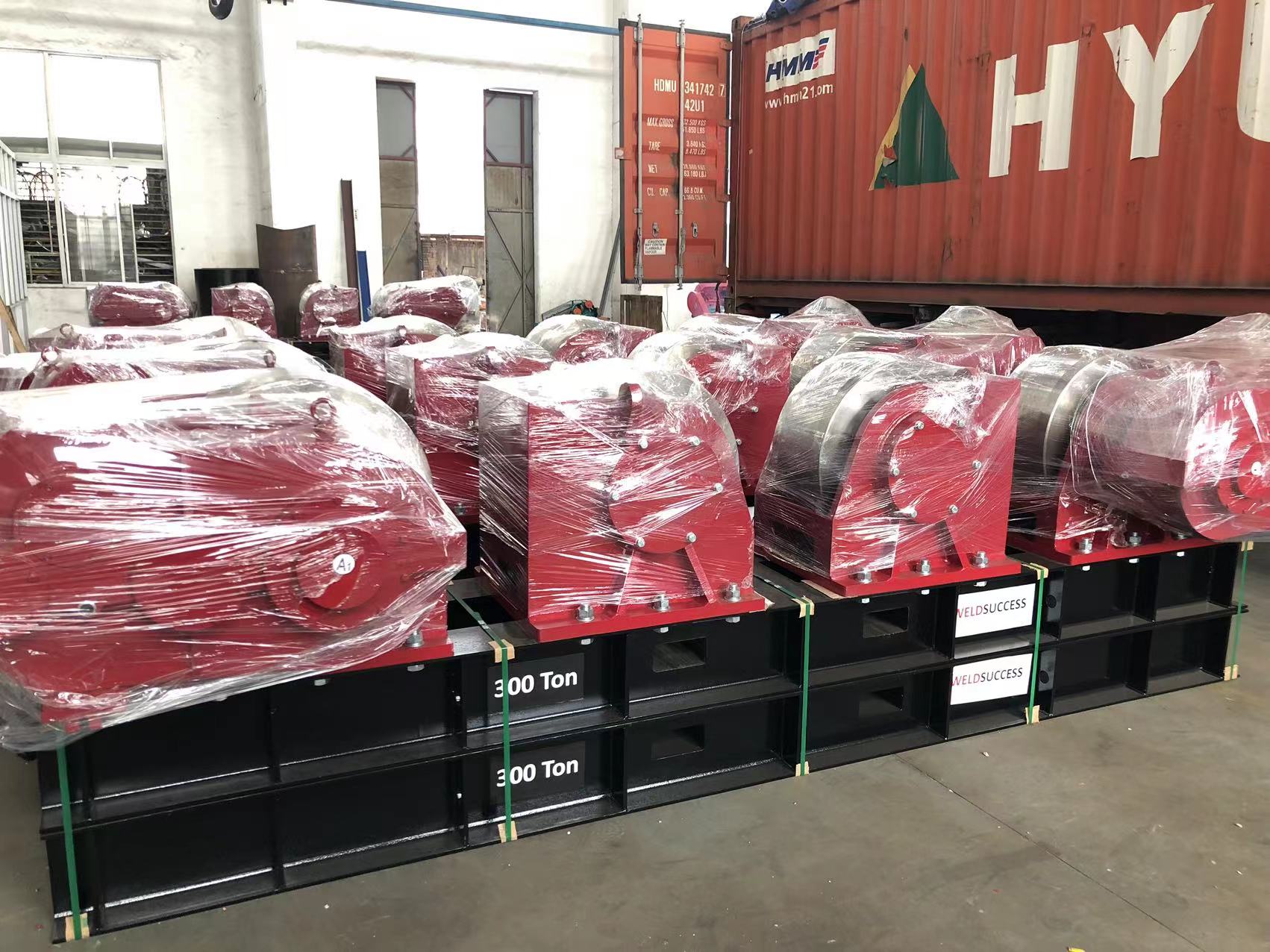
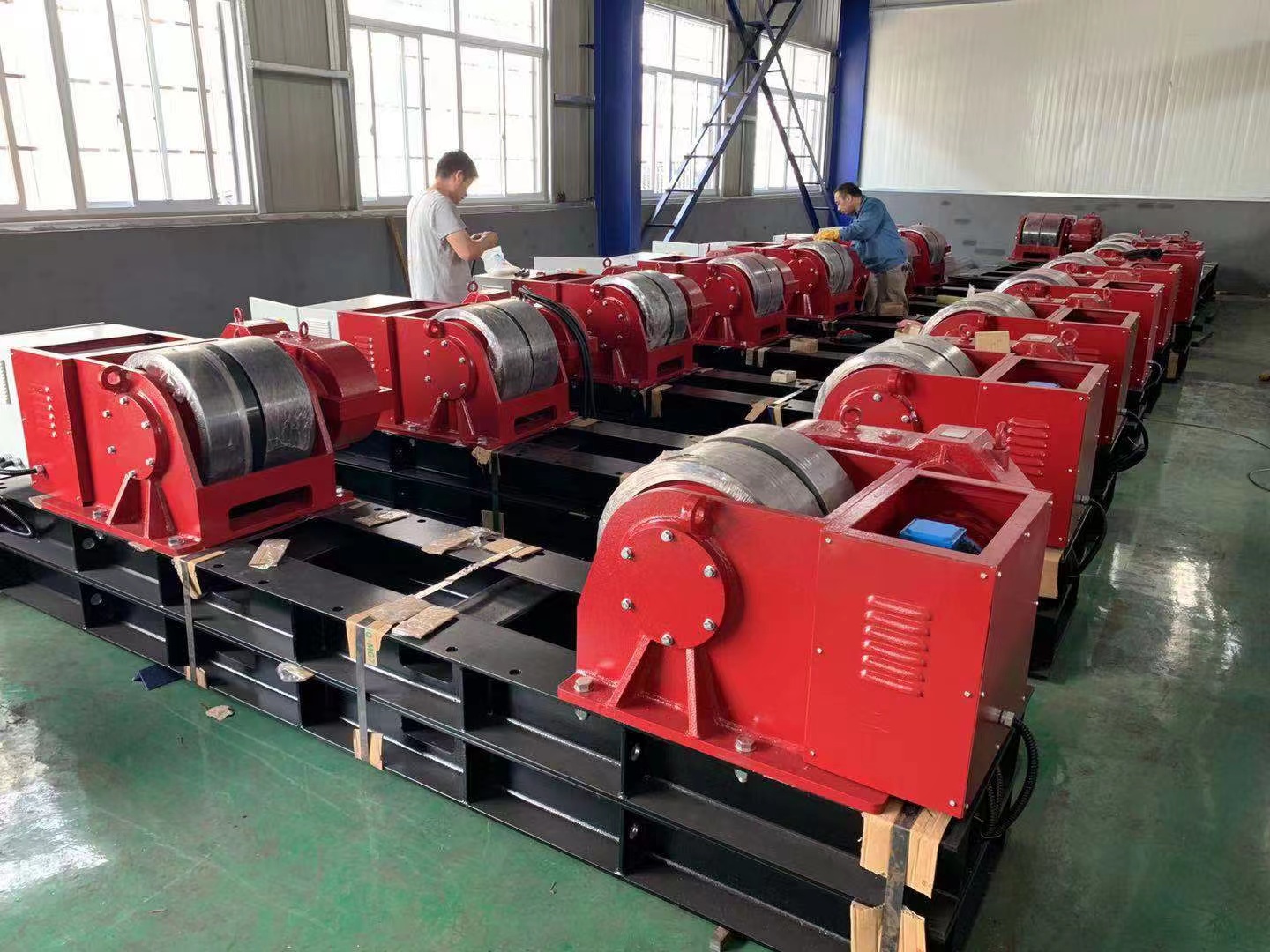
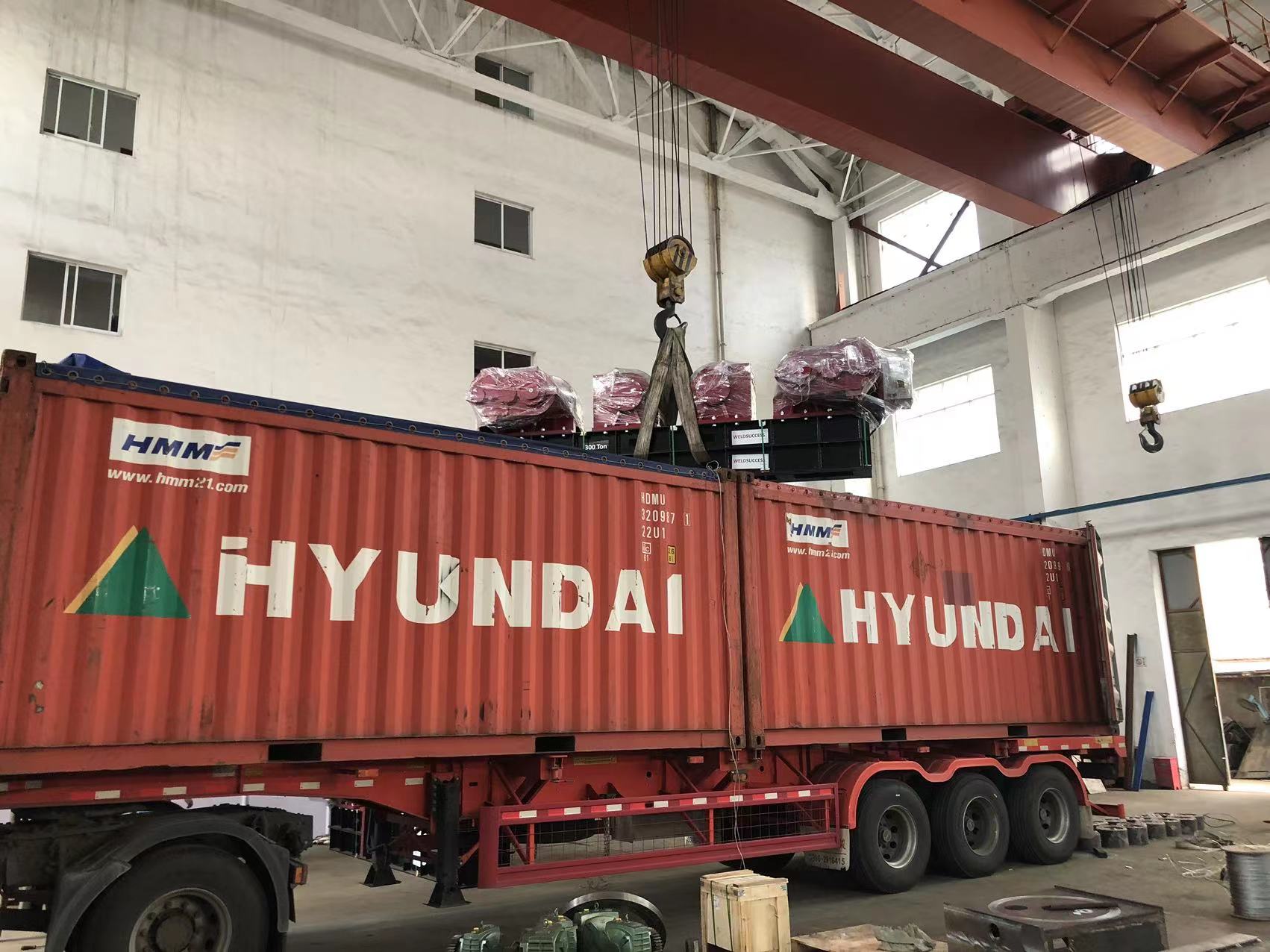
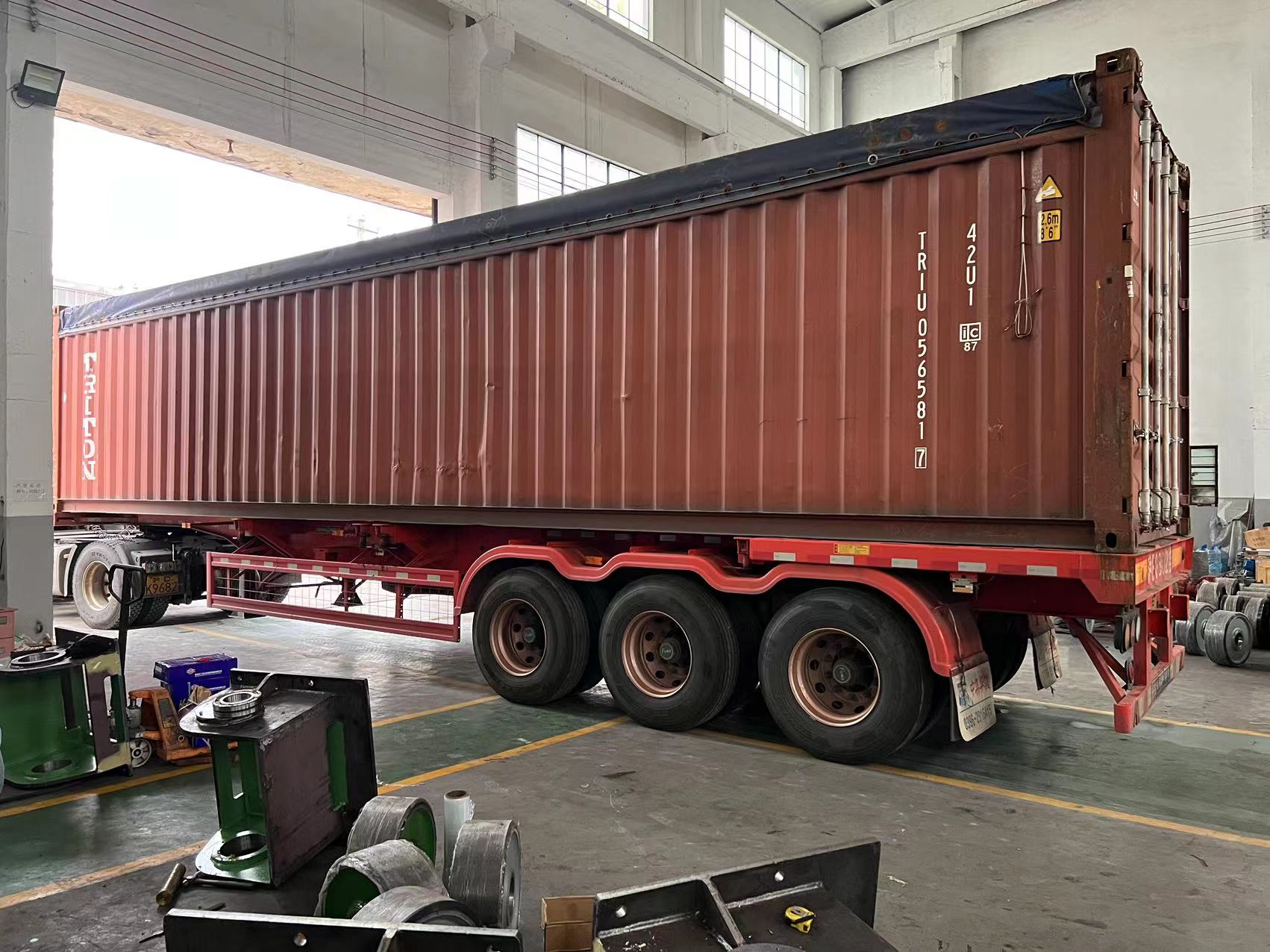
✧ Previous Projects
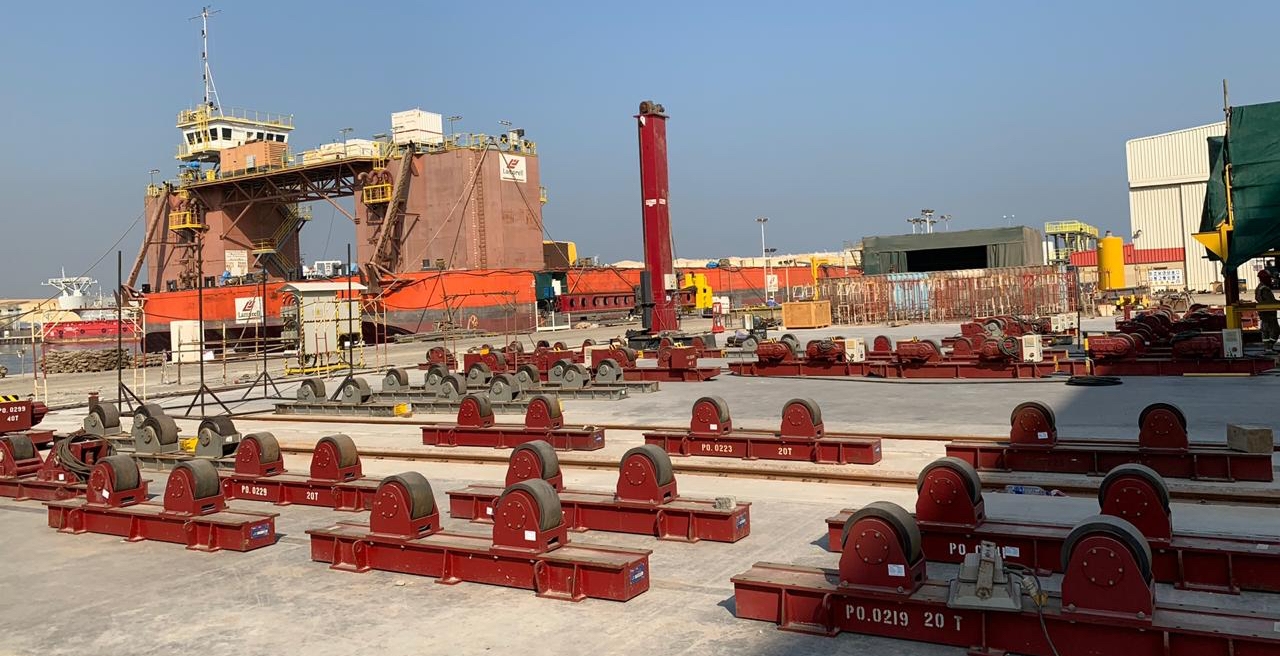

